INNOVATION

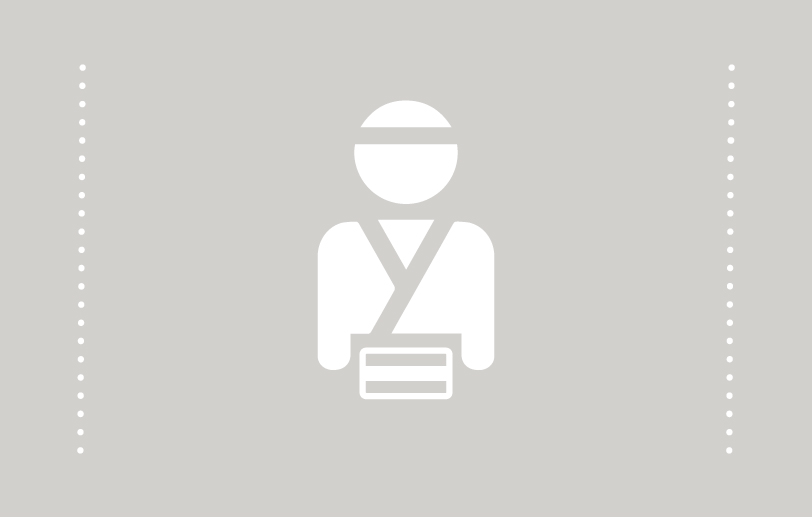
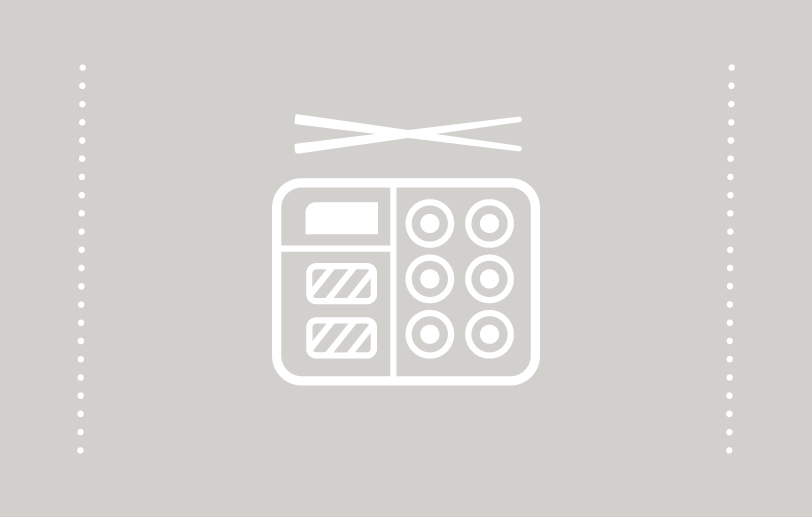
Super-Flexible Line
A New 'Manufacturing Sushi Shop' for Efficient Mixed-Product / Varying-Volume Manufacturing
We asked ourselves whether we would be able to swiftly respond to an order for just a single part. The answer we came up with led to the creation of the super-flexible line. Setup data for jigs and tools are simply loaded from a USB stick so programs can be easily changed. This is combined with a 'free-address utilization' of processing machines. On the Super-flexible Line, we are able to produce different products starting from a batch size of 1. The line can produce small quantities across a wide variety of parts without the need to maintain extra stock.
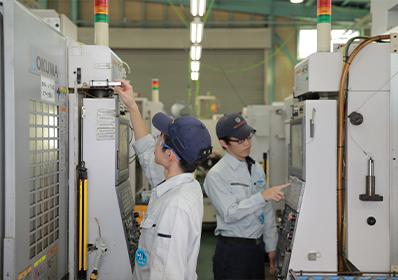
Program Data Transferal Using USB
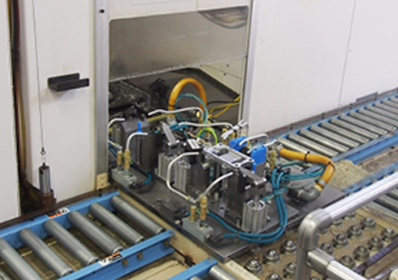
Scene of External Jig Changeover
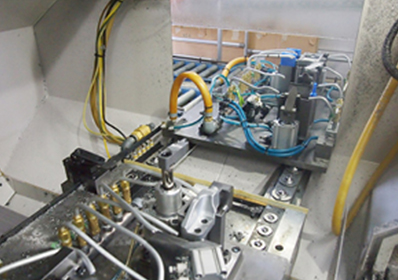
Switching from A Parts to B Parts
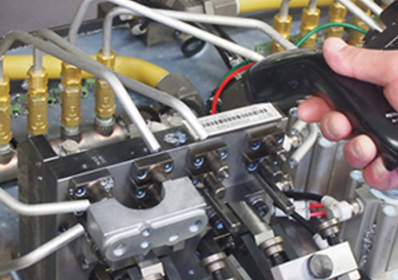
Consistency Check with Barcodes during Changeovers
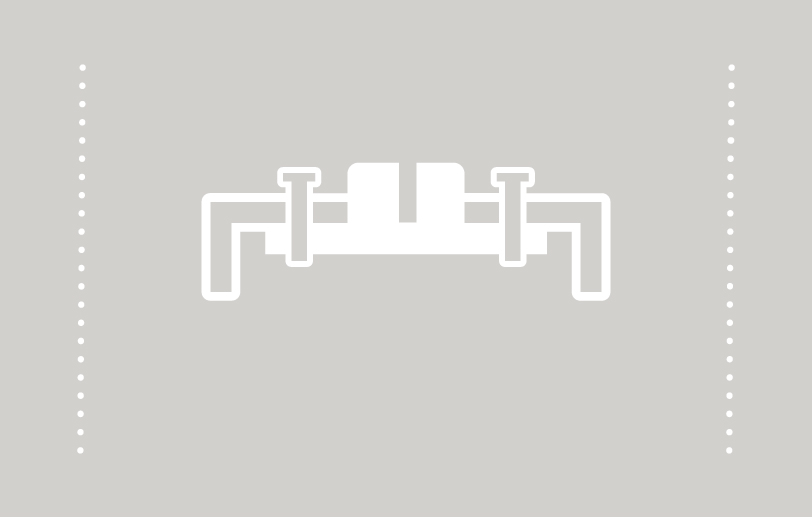
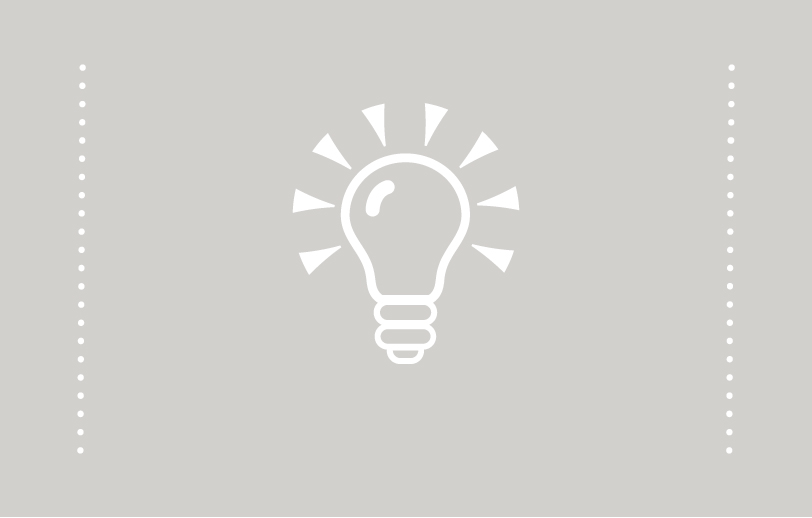
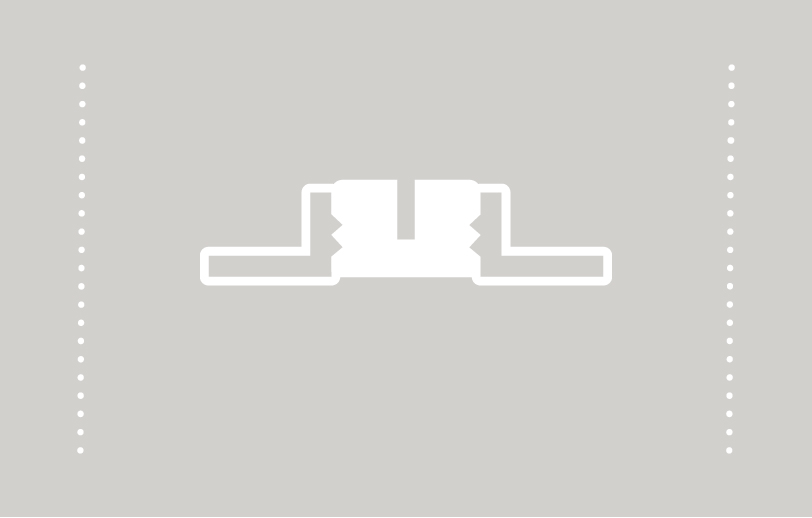
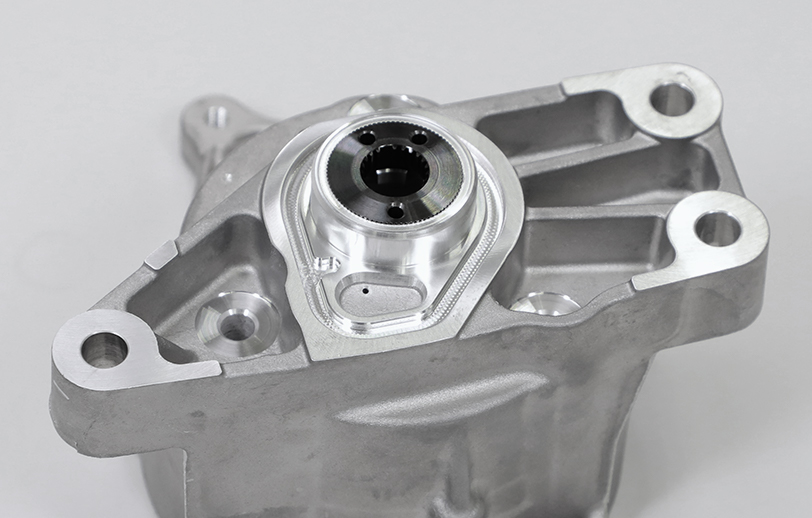
Plastic-Flow Binding
Replacing Bolts with a New Joining Method
Plastic-Flow Binding is a technology that was developed by KSK in 2013. Aluminum die-cast parts lack ductility, i.e. the capacity for plastic deformation, but with this method for joining aluminum and steel parts, it is possible to cater to the increasing demand for low-cost and lightweight parts. The method is currently able to join aluminum die-cast parts to plastic and copper, providing better options for joining different materials together and enabling research and development into ever lighter parts, as well as parts designed for heat-dissipation.
34 %
Cost Reduction
18 %
Weight Reduction
Award 2015
In 2015 KSK Received the JSTP Technology Development Award.
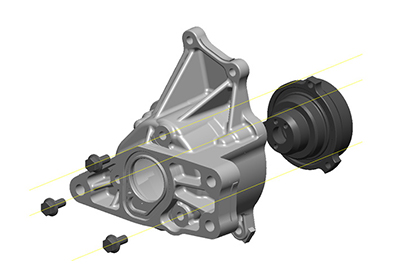
Old Product (Bolt Binding)
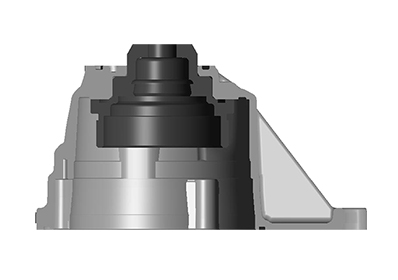
Cross-Section of Old Product
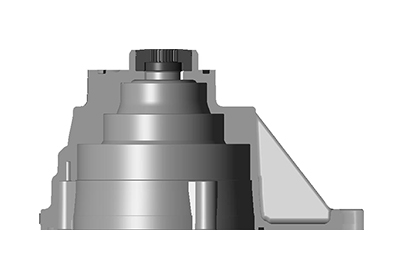
Cross-Section of Current Product
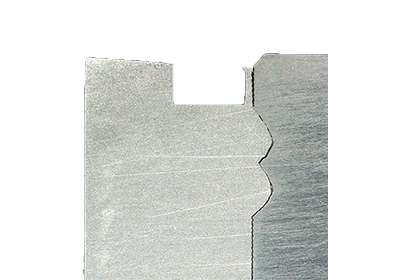
Plastic-Flow Binding Area

Binding Resin and Alunimum
Advancing the Technology for Further Weight Reduction
KSK has enhanced its Plastic-Flow Binding technology for joining aluminum die-cast parts and resin parts. Applying pressure to the aluminum makes it 'flow' into grooves in the resin section. This happens at room temperature without the need for pretreating the parts.




One-Motor Electric Shift Control
KSK Developed a Lightweight and Compact Electric Transmission Control.
Conventional AMT shift control systems required either two motors or three solenoids (or hydraulic solenoids) for shift and selection. By combining the motor that provides actuation with a clutch, KSK has enabled shift and selection operations to be carried out with a single motor. This reduces weight by 50-60% and halves the amount of space needed by conventional models. A prototype for small vehicles is currently being evaluated.
60 %
Weight Reduction
50 %
Space